Revolutionizing Manufacturing: The Power of 3D Rapid Prototyping
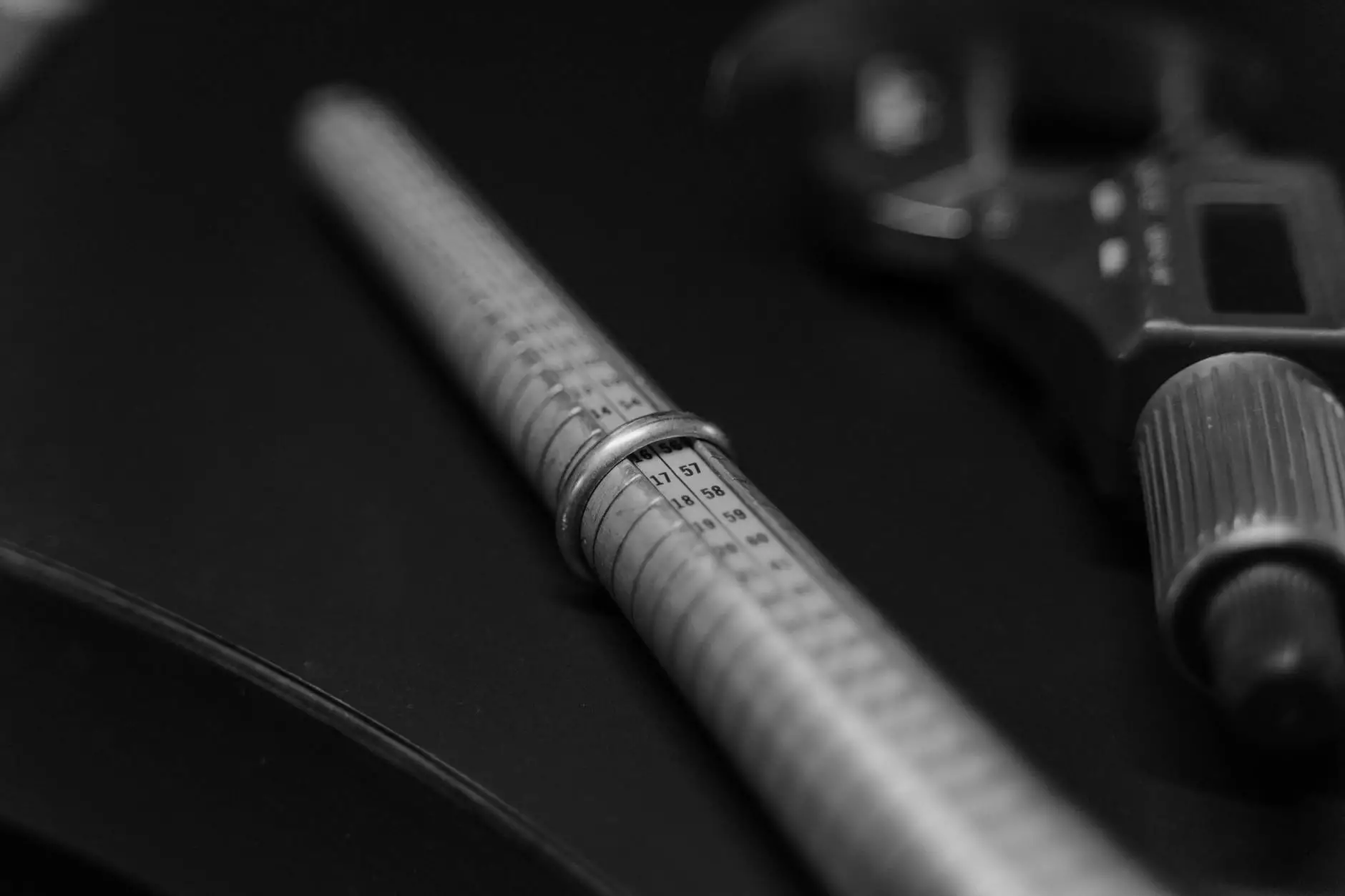
In the contemporary industrial landscape, the significance of 3D rapid prototyping cannot be overstated. This innovative method has become a cornerstone for businesses, especially in the realm of metal fabrication. By harnessing the capabilities of 3D rapid prototyping, manufacturers can significantly enhance their productivity, efficiency, and product quality, making it essential for any company aiming to stay competitive in today's fast-paced market.
The Fundamentals of 3D Rapid Prototyping
At its core, 3D rapid prototyping is a process that allows designers and engineers to create physical models from 3D computer-aided design (CAD) data. This process is exceptionally fast, allowing for the production of prototypes in a fraction of the time compared to traditional manufacturing techniques.
How Does 3D Rapid Prototyping Work?
The process typically involves several key steps:
- Design Creation: The product's design is created using CAD software.
- Slicing: The CAD model is sliced into thin horizontal layers, allowing the printer to know how to construct the object layer by layer.
- Printing: Using various additive manufacturing techniques, the prototype is built layer by layer.
- Finishing: Once printed, the prototype may undergo finishing processes including sanding, polishing, or painting to achieve the desired aesthetic and functional properties.
Benefits of 3D Rapid Prototyping in Metal Fabrication
The utilization of 3D rapid prototyping in metal fabrication brings a multitude of benefits, which can drastically improve product development cycles and final outcomes.
1. Increased Speed to Market
One of the most significant advantages is the reduced time-to-market. Traditional prototyping methods can take weeks or even months. However, with 3D rapid prototyping, prototypes can often be produced in a matter of hours, enabling companies to test concepts and iterate designs quickly.
2. Cost Efficiency
3D rapid prototyping also offers exceptional cost savings. The traditional methods of prototyping often require expensive tools and initial investments. In contrast, 3D printing technologies can produce components directly based on digital designs, which minimizes waste and reduces overall production costs.
3. Design Flexibility
The design flexibility that comes with 3D rapid prototyping is unparalleled. It allows for complex geometries that are often impossible or prohibitively expensive to create using conventional methods. This flexibility enables innovation and allows engineers and designers to experiment with new designs without the fear of incurring significant costs.
4. Enhanced Collaboration
Rapid prototypes can be created quickly and shared among teams, fostering collaboration between designers, engineers, and stakeholders. This immediacy facilitates timely feedback and accelerates decision-making processes.
5. Improved Quality and Testing
With the ability to produce prototypes rapidly, companies can engage in rigorous testing sooner in their development cycle. This early testing allows for the identification of design flaws and issues, which can be rectified before full-scale production begins, improving the overall quality of the final product.
Applications of 3D Rapid Prototyping in Metal Fabrication
The applications of 3D rapid prototyping are vast, particularly in metal fabrication. Here are some notable applications:
1. Automotive Industry
In the automotive sector, 3D rapid prototyping is used to create functional parts and components for testing new designs. This has revolutionized the way automotive companies approach design and engineering, allowing them to innovate rapidly and efficiently.
2. Aerospace Engineering
The aerospace industry has seen transformative changes due to 3D rapid prototyping. Components that are lightweight and durable can be produced quickly, facilitating advances in aircraft design and enabling more rigorous testing of prototypes under real-world conditions.
3. Medical Devices
In healthcare, 3D rapid prototyping is instrumental in creating medical devices and prosthetics tailored to specific patient needs. Bespoke solutions can be formulated, enhancing patient care and outcomes.
4. Custom Manufacturing
The ability to create custom prototypes rapidly allows businesses that require tailored solutions—such as machinery manufacturers or boutique design firms—to thrive. This caters to niche markets and specialized applications, making 3D rapid prototyping a vital tool in their arsenal.
Choosing the Right 3D Rapid Prototyping Technology
When considering 3D rapid prototyping, it's essential to select the right technology. Various methods exist, each suited to different materials and applications. Here are some of the predominant technologies:
- Fused Deposition Modeling (FDM): Ideal for creating prototypes from thermoplastics, FDM is widely used due to its affordability and accessibility.
- Stereolithography (SLA): This process uses UV light to cure liquid resin into solid plastic, offering high precision and a smooth finish.
- Selective Laser Sintering (SLS): Utilizing a laser to fuse powdered materials, SLS is excellent for producing functional prototypes in a variety of materials, including metals.
- Direct Metal Laser Sintering (DMLS): Specifically designed for metals, DMLS allows the creation of complex metal parts directly from CAD data.
Integrating 3D Rapid Prototyping into Your Business Strategy
For businesses exploring the integration of 3D rapid prototyping into their processes, several steps can facilitate a smooth transition.
1. Assessing Needs
Begin by assessing your product development needs. Identify where rapid prototyping could enhance your processes. Consider which types of prototypes would be most beneficial for your projects.
2. Investing in Technology
Invest in the appropriate 3D rapid prototyping technology that aligns with your product requirements. This may involve procuring printers, materials, and software to implement the process effectively.
3. Training Staff
Ensure that your team is trained on the new technologies and processes. This training will enable them to leverage the full capabilities of 3D rapid prototyping in their workflows.
4. Developing Prototyping Best Practices
Establish best practices for prototyping within your organization. Determine workflows, quality control measures, and collaboration strategies to optimize the rapid prototyping process.
Conclusion
In conclusion, the adoption of 3D rapid prototyping is not just a trend; it is a transformational force in the manufacturing world. With its ability to speed up production, reduce costs, and enhance quality, it is essential for businesses in metal fabrication and beyond. Embracing this technology will not only provide a competitive edge but also foster innovation and adaptability. As the industry continues to evolve, those who invest in 3D rapid prototyping are sure to be at the forefront of the manufacturing revolution.
3 d rapid prototyping